Helium is a distinct element that has garnered focus for its weightlessness and non-reactive nature, making it a vital gas in various commercial applications. One of the most fascinating aspects of helium is its utilization in leak detection, where it plays a critical role in ensuring the integrity of systems that require sealed seals. Helium leak detectors are specific machines designed to find even the tiniest leaks in vacuum systems, high-pressure equipment, and other confined spaces. With their capability to detect helium, these devices help ensure safety and efficiency across a diverse of industries, including manufacturing, aviation, and automotive.
In this article, we will examine the mechanics behind helium leak detectors and how they utilize the properties of helium to deliver consistent performance. Comprehending these machines not only sheds light on their working principles but also emphasizes their value in preventing financially damaging mistakes and securing product reliability. As we dig into world of helium leak detection, we will uncover the technology and methodologies that make these detectors indispensable in today’s high-pressure environments.
Grasping Helium Leak Detection Instruments
Helium leak detectors are specific tools used to find and measure losses in environments that need to maintain a negative pressure or positive pressure. These detectors use helium as a tracer gas due to its small atomic size, that enables it to readily leak through even minuscule pinholes or defects. The detectors are crafted to detect the amount of helium in a particular area, making them vital for fields where leak detection is necessary, such as medicinal manufacturing, electronics, and aviation.
The function of a helium leak detector includes introducing helium into the environment being examined. If there are leaks present, the helium will leak out and can be analyzed by the detector. These devices often utilize various methods to analyze and assess the helium, including mass spectrometry or thermal detection. The type of technology affects the sensitivity and timeliness of the detector, that is important for ensuring consistent performance and dependability in leak detection operations.
Using a helium leak detector offers major advantages over classic methods. Their precision enables the detection of leaks at levels that would be invisible with other gases, leading to improved quality control and security in production methods. As industries increasingly prioritize precision, the incorporation of reliable helium leak detectors has become a common practice, ensuring that systems are airtight and functioning at peak levels.
Key Features of Helium Leak Detectors
A major aspect of helium leak detectors is their sensitivity. These machines are designed to detect extremely small amounts of helium, often in the scale of ppb. This elevated level of sensitivity is essential for applications such as vacuum systems and sealed packages where even the tiniest leak can lead to significant issues. Helium's unique properties, including its light molecular weight and inert nature, make it an optimal candidate for detecting leaks in multiple systems.
Stable Performance Helium Leak Detector
Another important feature is the reliability of performance over time. A helium leak detector with stable performance ensures consistent and reliable readings, which is crucial for maintaining quality control in manufacturing processes. Many modern detectors come equipped with automatic calibration features that help maintain accuracy and minimize manual calibration. This reliability minimizes periods of inactivity and enhances the overall performance of the leak detection process.
User-friendliness is also a significant aspect of modern helium leak detectors. Many instruments are designed with intuitive interfaces, making it more straightforward for operators to manage their operations. Features such as graphical displays and intuitive controls allow for quick setup and monitoring, ensuring that operators with little technical background can effectively use the equipment. This accessibility is crucial in multiple fields, from automotive to aerospace, where personnel may require efficient tools to detect and manage leaks effectively.
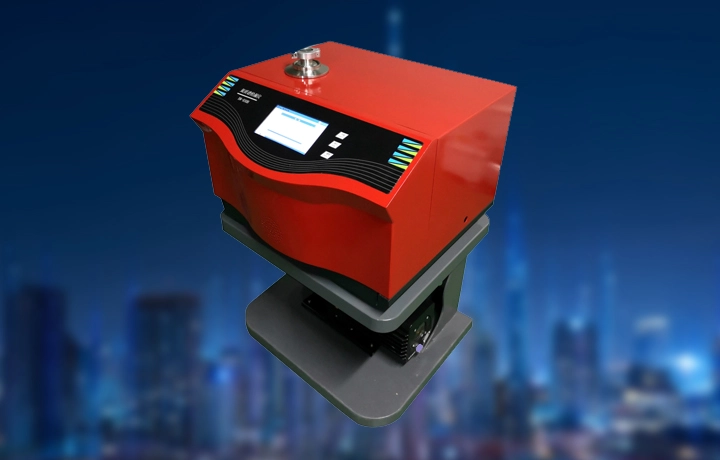
Applications of Helium Leak Detection
Helium leak detection is commonly used in the aerospace industry to ensure the integrity of fuel management systems, high-pressure areas, and survival systems. In applications where small leaks can lead to disastrous outcomes, the distinct properties of helium make it an optimal selection for leak testing. The reliable detection capabilities of helium leak detectors enable engineers ensure protection and conformance in the rigorous environment of aerospace engineering.
In the healthcare technology field, helium leak detection plays a critical role in ensuring the effectiveness and safety of various products such as syringes, respiratory devices, and diagnostic equipment. The precision of helium leak detectors permits manufacturers to find and fix leaks that could compromise the performance of these devices. This leads to higher quality standards and improves patient safety by ensuring that devices work properly without any risk of contamination.
Moreover, helium leak detection is important in the semiconductor production sector, where keeping a controlled environment is vital for producing premium components. Any leaks in vacuum systems can lead to impurities and loss of yield, making it imperative to use highly accurate helium leak detectors. The consistent operation of these machines enables manufacturers to monitor and ensure the safety of their processes, ultimately resulting in enhanced product dependability.